Fundamentals Braking Technology for Heavy Applications
페이지 정보

본문
Magnetic braking is a solution that has been rapidly advancing in recent years due to its immense efficiency and performance in various commercial applications. The underlying mechanism behind magnetic braking lies in utilizing electromagnetic interactions to create friction between two magnetic surfaces, effectively generating a braking effect. This technology has numerous benefits, making it a attractive choice for heavy industrial applications. In this article, we will delve into the key elements of magnetic braking and explore its potential in various industries.
The basic working principle of magnetic braking involves the interaction between a magnetic motor and a stationary magnetic receiver. When a magnetic field is applied to the stator, it creates a magnetic force that acts on the rotor, causing electromagnetic contact between the two magnetic surfaces. This frictional force creates the necessary braking effect, allowing the equipment to slow down or maintain its position.
One of the primary disadvantages of magnetic braking is its ability to provide a varying level of braking force, making it suitable for a wide range of applications. By adjusting the magnetic field strength, the level of friction can be controlled to provide precise braking. This characteristic makes magnetic braking an attractive choice for applications where variable braking is required, such as in crane technology.
Another significant benefit of magnetic braking is its low wear and tear on mechanical components. Traditional braking systems rely on fragile mechanical components, such as discs, which can lead to regular replacements and maintenance. Magnetic braking, on the other hand, achieves its braking effect through frictional contact, eliminating the need for high-maintenance components.
In heavy industrial applications, magnetic braking has several advantages. Firstly, it can be used to recapture energy, reducing energy consumption and waste. When a load is lowered or brought to a stop, the magnetic braking system can capture some of the kinetic energy and convert it into electrical energy, providing a feedback braking effect. This helps to reduce the equipment's energy consumption and environmental impact.
Magnetic braking also offers reduced safety in heavy industrial applications. In machinery such as hoists, the lack of mechanical components and the smooth operation of the braking system reduce the risk of mechanical failure and accidents. Additionally, the low-maintenance requirements of magnetic braking systems minimize dissatisfaction and improve overall equipment productivity.
Furthermore, magnetic braking technology is highly agile and suitable for конусный тормоз электродвигателя various applications. It can be implemented in various layouts, such as in-line, parallel, or off-axis, making it suitable for different types of machinery and equipment.
However, there are some hindrances associated with magnetic braking technology, particularly in terms of its cost and complexity. The initial expense required to implement magnetic braking systems can be substantial, which may deter some manufacturers and end-users. Additionally, the technology requires accurate control and monitoring to ensure maximum performance and safety.
In conclusion, magnetic braking is a highly efficient and dependable technology suitable for heavy industrial applications. Its ability to provide adjustable braking, low wear and tear on mechanical components, energy recapture, enhanced safety, and agility make it an attractive choice for manufacturers and end-users. As the hypothesis continues to evolve and improve, we can expect to see magnetic braking occupy a prominent role in various industries, including heavy machinery, equipment production, and clean energy.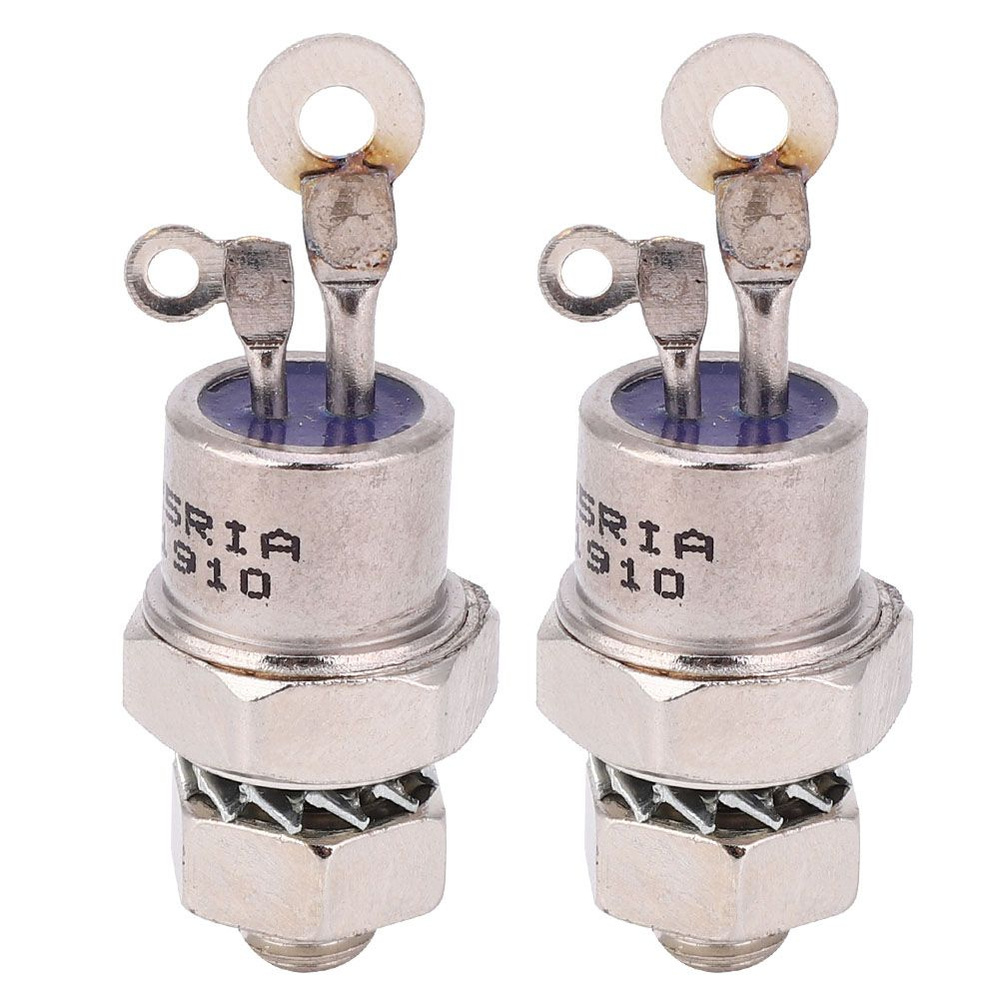
The basic working principle of magnetic braking involves the interaction between a magnetic motor and a stationary magnetic receiver. When a magnetic field is applied to the stator, it creates a magnetic force that acts on the rotor, causing electromagnetic contact between the two magnetic surfaces. This frictional force creates the necessary braking effect, allowing the equipment to slow down or maintain its position.
One of the primary disadvantages of magnetic braking is its ability to provide a varying level of braking force, making it suitable for a wide range of applications. By adjusting the magnetic field strength, the level of friction can be controlled to provide precise braking. This characteristic makes magnetic braking an attractive choice for applications where variable braking is required, such as in crane technology.
Another significant benefit of magnetic braking is its low wear and tear on mechanical components. Traditional braking systems rely on fragile mechanical components, such as discs, which can lead to regular replacements and maintenance. Magnetic braking, on the other hand, achieves its braking effect through frictional contact, eliminating the need for high-maintenance components.
In heavy industrial applications, magnetic braking has several advantages. Firstly, it can be used to recapture energy, reducing energy consumption and waste. When a load is lowered or brought to a stop, the magnetic braking system can capture some of the kinetic energy and convert it into electrical energy, providing a feedback braking effect. This helps to reduce the equipment's energy consumption and environmental impact.
Magnetic braking also offers reduced safety in heavy industrial applications. In machinery such as hoists, the lack of mechanical components and the smooth operation of the braking system reduce the risk of mechanical failure and accidents. Additionally, the low-maintenance requirements of magnetic braking systems minimize dissatisfaction and improve overall equipment productivity.
Furthermore, magnetic braking technology is highly agile and suitable for конусный тормоз электродвигателя various applications. It can be implemented in various layouts, such as in-line, parallel, or off-axis, making it suitable for different types of machinery and equipment.
However, there are some hindrances associated with magnetic braking technology, particularly in terms of its cost and complexity. The initial expense required to implement magnetic braking systems can be substantial, which may deter some manufacturers and end-users. Additionally, the technology requires accurate control and monitoring to ensure maximum performance and safety.
In conclusion, magnetic braking is a highly efficient and dependable technology suitable for heavy industrial applications. Its ability to provide adjustable braking, low wear and tear on mechanical components, energy recapture, enhanced safety, and agility make it an attractive choice for manufacturers and end-users. As the hypothesis continues to evolve and improve, we can expect to see magnetic braking occupy a prominent role in various industries, including heavy machinery, equipment production, and clean energy.
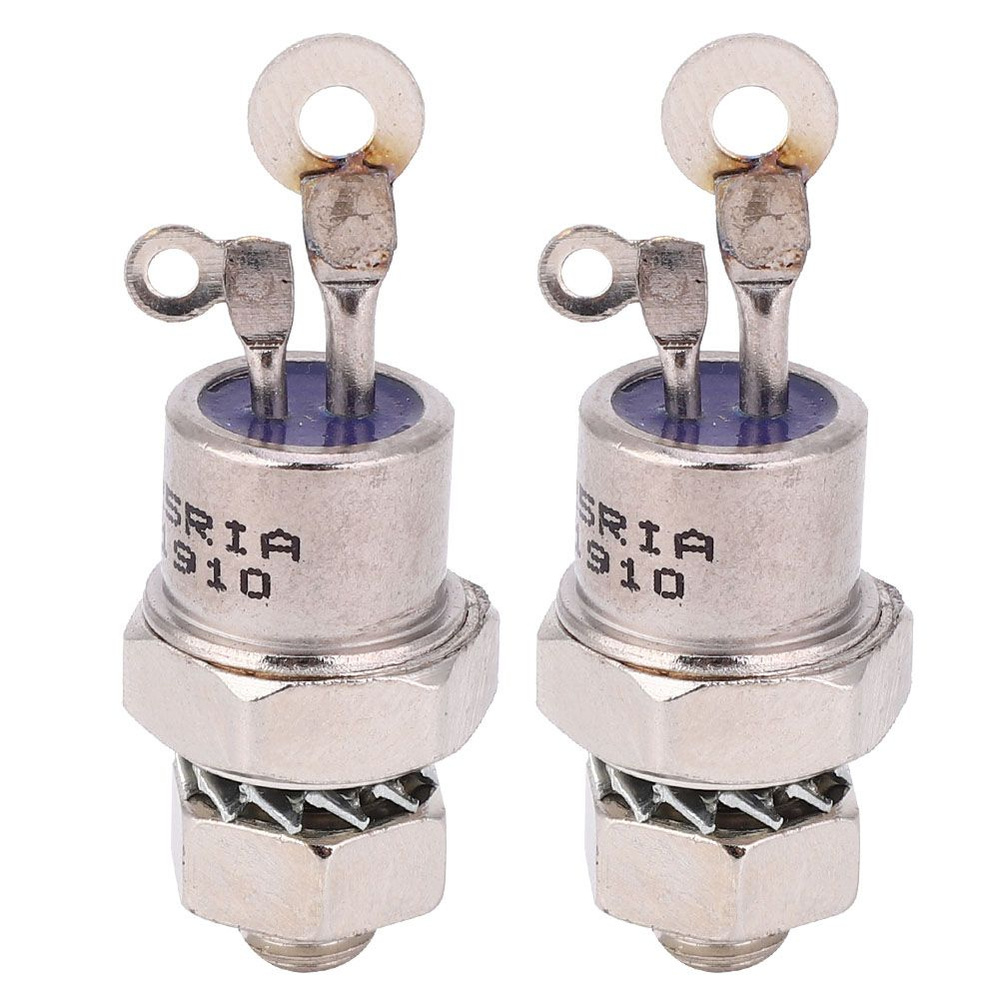
- 이전글{DIY Woodworking Project for a {Wooden|Finished|Homemade} Bookshelf With the rise of {urban living|city living|condensed living} and the continuous growth of {compact spaces|cozy homes|small dwellings}, the need for {multi-functional furniture|practical p 25.03.28
- 다음글The Most Pervasive Problems In Cut Key For Car 25.03.28
댓글목록
등록된 댓글이 없습니다.